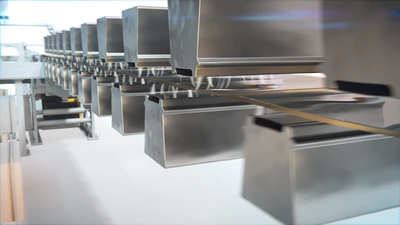
Simultane beidseitige Elektroden-Beschichtung
06.08.2020
Führend in der Entwicklung und Herstellung von Batterieelektroden
Dürr Megtec treibt die Entwicklung und Herstellung von Batterieelektroden stetig voran. Eric Maki, Development Center Manager, und David Ventola, Director Business Development – Engineered Products, der Dürr-Division Clean Technology Systems (CTS) in De Pere (Wisconsin, USA) stecken mitten im Forschungsprozess für optimierte Verfahrenstechniken und -lösungen im Wachstumsfeld Batterien. Die nachstehenden Argumente unterstreichen, weshalb sie davon überzeugt sind, dass die in unterschiedlichen Größen verfügbaren Dürr Megtec-Anlagen zur beidseitigen Beschichtung eine bessere Elektrodenqualität sowie geringere Betriebskosten im Vergleich zu Konkurrenzprodukten auf dem Markt ermöglichen.
Die Elektrodentechnik im Inneren jeder Lithium-Ionen-Batterie besteht unabhängig von deren Verwendungszweck aus einer Metallfolie, die auf beiden Seiten mit Aktivmaterial in Form einer Paste beschichtet wird. Als Substrat wird Aluminiumfolie für positive Elektroden (Kathode) und Kupferfolie für negative Elektroden (Anode) verwendet. Diese beschichteten Elektroden sind essenziell für die Funktion der Batterie. Dementsprechend führt eine mangelhafte Beschichtung zu einer fehlerhaften Batterie. Aus diesem Grund muss der gesamte Beschichtungsprozess extrem präzise sein und streng kontrolliert werden.
Eine typische Beschichtungspaste setzt sich aus Lithiumsalzen, die in einem Lösungsmittel in Elektronikqualität gelöst sind sowie in Wasser aufgelöstem Grafit zusammen. Das Gemisch wird über Breitschlitzdüsen beidseitig auf die Folien aufgetragen. Die Folie verläuft über eine stützende Präzisionsedelstahlwalze, mit deren Hilfe die Folie geführt und eine solide Basis für eine präzise Nassschicht bereitgestellt wird.
Um eine optimale Batterieleistung zu erzielen, muss jeder Schritt im Beschichtungsprozess kontrolliert werden – vom Umgang mit dem Pulver über das Mischen der Paste bis hin zum Beschichten und Trocknen. Die größte Herausforderung beim Beschichten mithilfe einer Breitschlitzdüse und einer stützenden Walze liegt jedoch beim beidseitigen Auftragen des Gemischs auf die Folie.
Beim herkömmlichen Prozess kann immer nur jeweils eine Folienseite beschichtet werden. Bei einem solchen Fertigungsaufbau sind zwei Durchläufe durch dieselbe Linie einer Beschichtungsanlage erforderlich. Effizienter ist es, beide Seiten in einem Durchlauf zu beschichten. Hierzu gibt es zwei Möglichkeiten: 1) ein sequenzielles oder Tandem-Beschichtungssystem oder 2) die simultane beidseitige Beschichtung
Eric Maki, Development Center Manager, Dürr - Clean Technology Systems (CTS)
Die Ingenieure bei Dürr Megtec in De Pere haben sich für die zweite Möglichkeit entschieden: Sie haben für diesen Anwendungsfall das sogenannte „Tensioned Web“-Beschichtungsverfahren weiterentwickelt. Dabei werden mithilfe einer vertikal befestigten Breitschlitzdüse gleichzeitig beide Seiten der horizontal verlaufenden Elektrodenfolie beschichtet. Bei diesem Prozess wird ein gleichmäßiges Beschichtungsgewicht aufgetragen, das genau dem Beschichtungsgewicht bei Verwendung einer stützenden Präzisionswalze entspricht.
Die simultane beidseitige Elektrodenbeschichtung ermöglicht Batterieherstellern eine höhere Produktionseffizienz. Zu den Vorteilen zählen hierbei:
- effektive Verdopplung des Durchsatzes im Vergleich zur einseitigen Beschichtung
- Notwendigkeit nur eines einzelnen Trocknungsdurchgangs: Dies bedeutet auch, dass keine Seite zwei Mal getrocknet wird und somit die Trocknung von Ober- und Unterseite identisch ist
- geringerer Platzbedarf auf der Produktionsfläche und in der Höhe im Vergleich zu Tandem-Anlagen: Gesamtlänge 5 bis 10 Meter kürzer, Gesamthöhe 5 bis 6 Meter geringer
- 30 bis 50 % geringere Investitions- und Betriebskosten im Vergleich zu Tandem-Anlagen
- größere Bandbreite an Beschichtungsgewichten für Lithium-Ionen-Pasten möglich
- Prinzip bedingt können sich im Spalt zwischen Walze/Folie und Breitschlitzdüse bei der Beschichtung der zweiten Seite keine Partikel fangen (keine Schlieren oder Folienrisse)
- geringere Probleme mit Falten am Beschichtungspunkt
Verbesserte Effizienz, gesteigerte Leistung und optimierte Anwendung
In der Energiespeicherbranche sind reduzierte Fertigungskosten in Verbindung mit gesteigerter Leistung und verbesserter Produktqualität gefragt. Um diese Ziele zu erreichen, müssen die Fertigungsanlagen zum Herstellen großer Mengen an Lithium-Ionen-Zellen jedoch erheblich angepasst und ausgebaut sowie die Leistung der einzelnen Anlagenlinien gesteigert werden. Zugleich gewinnen die Vorteile der simultanen beidseitigen Beschichtungstechnik immer mehr an Bedeutung, je größer und schneller Anlagenlinien für die Beschichtung werden sollen.
Diese Dynamik bei der Markteinführung sieht David Ventola als Grund dafür an, dass sich Batteriehersteller für Lösungen zur Beschleunigung des Übergangs von Forschung & Entwicklung zur Massenfertigung von Elektroden für Lithium-Ionen-Batterien an Dürr Megtec wenden.
Wir bieten eine große Bandbreite von Anlagenlinien zur Beschichtung an. Von einer einfachen Laboranlage zur Beschichtung, die speziell für kurze Fertigungsläufe konzipiert ist, bis hin zum GigaCoater™-System mit einer möglichen jährlichen Leistung von 2 bis 3 Gigawattstunden (Gwh) pro Anlage
David Ventola, Director Business Development- Engineered Products, Dürr - Clean Technology Systems (CTS)
Anders ausgedrückt entspricht dies einer Batterieelektroden-Kapazität von 5 Stunden Backup-Stromversorgung für 300.000 Haushalte (basierend auf einem durchschnittlichen Verbrauch von 2 kWh) oder für den Energiespeicher von 30.000 batteriebetriebenen (mit 100 kWh konfigurierten) Elektrofahrzeugen.
In der stetig wachsenden Branche der Lithium-Ionen-Batterien steigt auch der Druck zur Senkung der Kosten kontinuierlich. Mit dem simultanen beidseitigen Beschichtungsprozess erzielen Batteriehersteller eine höhere Kosteneffizienz und werden dadurch wettbewerbsfähiger. Durch eine beschleunigte Markteinführung von Lithium-Ionen-Batterien gelingt es Herstellerfirmen, ihre batteriebetriebenen Produkte ohne Zeitverluste an ihre Kunden zu liefern.
Dank der Kompetenz von Dürr gelingt es Batterieherstellern ihr Geschäft auszubauen und die steigende Nachfrage nach Endnutzergeräten für Lithium-Ionen-Batterien zu decken. Wenn Sie also das nächste Mal ein batteriebetriebenes Gerät verwenden – wahrscheinlich noch heute – dann denken Sie daran, dass Dürr Teil der Technik im Inneren ist.
Erfahren Sie mehr über die Herstellung von Elektroden für Lithium-Ionen-Batterien: https://www.durr-megtec.com/en/industries/li-ion-battery-electrode-manufacturing.