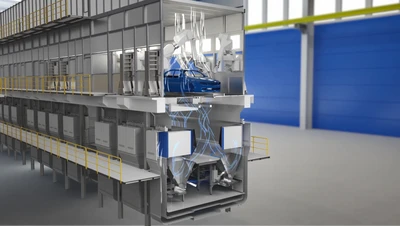
Fully automatic solution for maximum efficiency
Aug 5, 2020
EcoDryScrubber: A decade ago, Dürr revolutionized paint overspray separation with a sustainable process involving neither water nor chemicals.
Dry overspray separation was a real innovation in 2010. The EcoDryScrubber technology, a new development from Dürr at the time, gained popularity very quickly. This is hardly surprising given the high efficiency of the process in more ways than one.
The → EcoDryScrubber uses finely ground limestone powder to separate paint overspray. In filter modules installed in the booth substructure, air jets briefly whirl up the binding material. It is then picked up by the air flow, and deposited as a fine protective layer on all surfaces inside the filter modules as well as on the filter elements. The overspray carried into the modules by the process air from the spray booth is sucked in by the filters, but adsorbed into the limestone powder layer before getting that far. The flow direction is reversed at regular intervals to blow off the paint and limestone powder mixture. The falling material is collected in the hoppers and sucked into a piping system for disposal.
The filtration is so effective that the measurement methods currently available are unable to detect the presence of particles in the air flow. This means that up to 80 to 95 percent of the filtered process air can be reused, largely eliminating the need for the energy-intensive conditioning of fresh air. At the same time the use of water and chemicals is eliminated, unlike conventional wet separation where a constant supply of these consumables is needed. And there is no special waste to dispose of, since no paint sludge is produced.
Fully automatic control
While conventional wet separation requires ongoing process checks and adjustment of the chemicals used to the process, dry separation does not. The software versions installed since 2015 also feature an intelligent control concept and continuously adapt the separation process to the current painting tasks. This automatic system reduces manual interventions to a minimum and optimizes the consumption of limestone powder.
Straightforward supply and disposal worldwide, with the option of recycling
Limestone is a natural product that is mined and processed into limestone powder throughout the world. It is mainly used in cement production and in the pigment industry, but also in the food and pharmaceutical industries, and therefore is available worldwide via a dense production network. The limestone is delivered in trucks and stored in silos that can supply several painting lines. Bulk bags can also be used as an alternative material handling method. Reusing the limestone powder, for example as a secondary raw material in the cement industry or even in power plants for flue gas desulfurization, ensures that the cycle may be described as waste-free.
Suitable for universal use and winner of multiple awards
A particular strength of the EcoDryScrubber is its suitability for universal use since it can be used anywhere in the world regardless of the type of paint and the application technology. The EcoDryScrubber has won multiple awards for its high energy efficiency, including the environmental award given by the state of Baden-Württemberg, the SURCAR Innovation Award, and the Automotive News PACE AWARD in the category “Manufacturing Process and Capital Equipment”.
To date, the EcoDryScrubber from Dürr is already in use by numerous car manufacturers in over 80 lines. In 2010, BMW in Regensburg was the first OEM to opt for the new technology, and is still using it successfully in its paint shop to this day. One of the most recent EcoDryScrubber installations was at Škoda in Mladá Boleslav. The construction of the paint shop there was one of Dürr’s largest European projects in recent years. Škoda is exploiting the technology’s full potential in terms of sustainability: the company uses the paint-saturated limestone from the dry filters as a desulfurization additive for its own power plant – proof of the technology’s zero waste credentials.
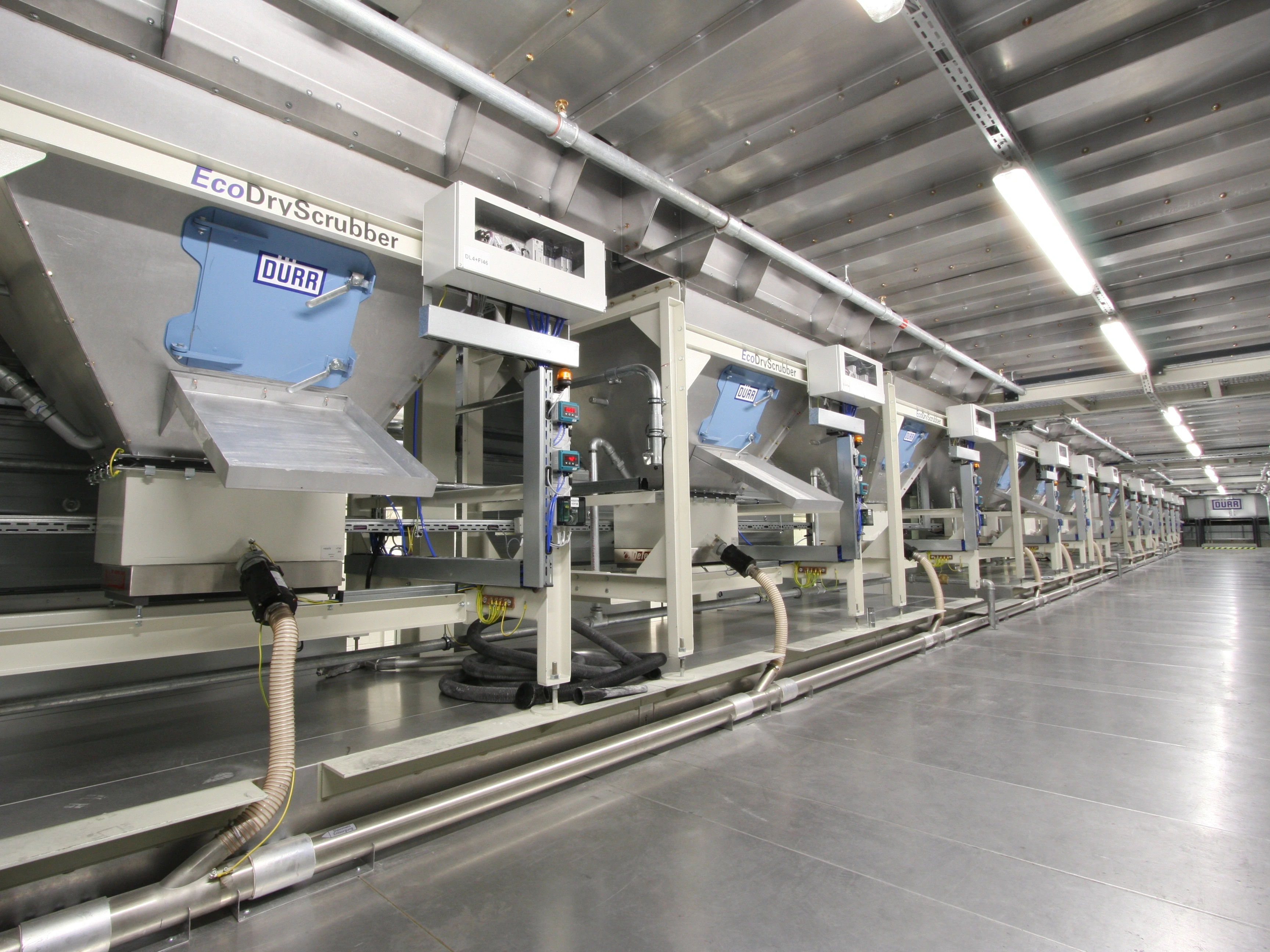
Find out more about the 10th anniversary of dry separation in our article → 10 years of dry separation. Part three of the series, which is about the EcoDry X and EcoDry Rack will be published this autumn.