EcoInCure – Innovative car body curing from the inside
EcoInCure stands for a new generation of car body curing: The heating and cooling of the car body take place primarily from the inside.
Best surface quality
EcoInCure’s air flow control produces the best possible top coat appearance. The car body is heated up from the inside, resulting in even heating and cooling conditions. Consequently, flow velocities on the outer body surface are minimal, greatly improving the appearance and distribution of the top coat and thus the surface quality. Leading paint suppliers have proven with their own research that paint curing with EcoInCure produces less waves and significantly improves quality.
Best process times
The principle of heating from the inside reaches massive car body components of the framework, e.g. rocker panels, more directly than conventional systems. This means optimum heat transfer from the hot air flow to difficult-to-access parts/areas. What’s more, it reduces the required process time for heating up the body by up to 30%.
Best for EVs
Electric vehicles need – among other things – well-reinforced rocker panels to protect the batteries in the event of a side impact. EcoInCure dries these rocker panels with their increased material thickness far better than conventional ovens, and prevents overheating in thinner parts of the body shell.
The same goes for future multi-substrate car body generations with new material combinations and new joining methods. Here, specifically, the new EcoInCure drying method reduces thermal component stresses to ensure increased process reliability.
And how does it work?
With EcoInCure the bodies run through the line transversely in stop and go operation. Only this conveying principle enables the direct inflow of hot curing air into the windshield opening. Jet nozzles with long throw distances aim into the interior of the car body and as a result, heat and cool the structure and painted body-sheets from the inside-out. The result is a very gentle but effective heating process along with significantly improved top coat appearance.
Minimized heating gradients and uniform temperature distributions within all car body compounds allow stress-reduced curing and consequently increase process reliability. Additionally available recirculating air modules enable custom-modelled processes for type-specific heating and cooling.
The EcoInCure heating concept is based around a central heat exchanger. Instead of local heat exchangers in the circulating air units, centrally heated curing air is admixed into every single recirculation air unit. This principle allows precise control of the temperature with low response time and reduced pressure losses across the whole heating cycle.
EcoInCure benefits
With EcoInCure, temperature and volumetric flows can be adapted individually. Custom heating and cooling processes can be defined for each body thanks to EcoInCure’s cyclic mode of operation and the option to assign a separate unit to each module.
EcoInCure's centrally heated air is distributed to each recirculating air unit and admixed into the curing air. Since the recirculating air units require no heat exchangers, pressure losses are significantly lower, which in turn reduces total electrical energy consumption by 25%.
Bodies pass through transversely. This layout saves a great deal of space, halving the dryer length of EcoInCure compared to conventional dryers. Less steel work is necessary directly above the ovens. The recirculating air units are located on the oven level.
DXQcontrol continuously tracks the drying conditions of each body, both during the paint drying process and during steel and aluminum bake-hardening. Each body receives its own individual, software-supported quality certificate.
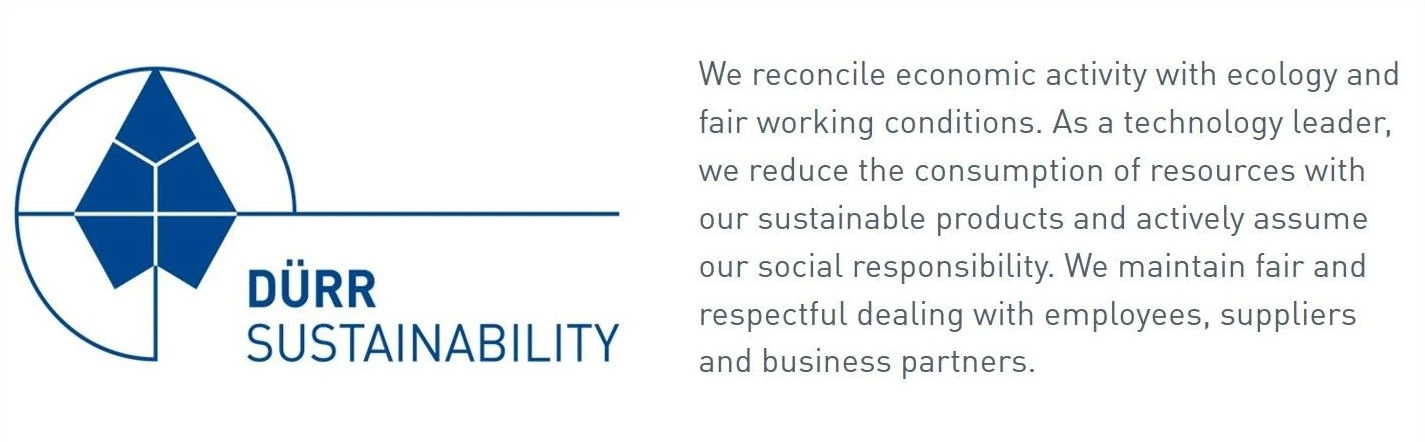