EcoProBooth – One spray booth for all painting tasks
Whether for interior painting, exterior painting, base coat or clear coat application, the new Dürr spray booth combines all painting tasks in an integrated plant and application technology system. EcoProBooth sets new standards in terms of energy consumption and efficiency with its well-thought-out recirculated air system and a novel approach to maintenance. This standardized box provides maximum flexibility for painting any type of vehicle from a compact car to an SUV thanks to the parallel box configuration of the spray booths.
Interior and exterior painting efficiently combined
The EcoProBooth, together with the EcoBell4 Pro Ux, allows vehicle interiors and exteriors to be painted in the same booth. The universal atomizer produces narrow jets for the inside of the body and wide jets for the outside and for metallic paints. As a result, all the painting tasks can be carried out in one box. This means that no time is wasted moving the bodies from one spray booth to another. Tasks are distributed, allowing inactive robots to be cleaned or maintained without interrupting production. The robots can move to integral service cubicles located in each corner of the spray booth for this work. Fresh air continuously flows through these cubicles, which means employees can access them at any time without breathing apparatus. As many of the servicing tasks can be performed without stopping production, this significantly increases the availability of the spray booth.
Maximum air recirculation rate, minimum energy requirement
EcoProBooth maximizes the air recirculation rate, using only 5% fresh air and thereby minimizing energy demand and CO2 emissions. After being freed from paint particles in a dedusting process, the air is efficiently and inexpensively reconditioned in the associated EcoDryScrubber dry paint overspray separation system by a convection heater box assigned directly to the spray booth.
Flexible box for all scenarios
The size of the booth allows all types of cars to be painted, from compact models to SUVs, but it can easily be expanded to take pickups and vans.
Instead of being used in a linear layout with unchanging cycle times, the painting box can be repurposed for a parallel production layout such as Dürr’s "paint shop of the future". This flexibility allows the painting process to be tailored to the current vehicle models and scaled and upgraded as needed.
Advantages
- Simple scaling, straightforward conversion and maximum flexibility thanks to standardized spray booth
- Higher availability through rapid maintenance in service cubicles without interrupting production
- No need to access the application area on production days
- Energy savings through maximum air recirculation rate
- Energy consumption 75% lower than with a wet scrubber
- Energy consumption 40% lower than with a conventional dry scrubber
- Efficient use of resources in the modular “paint shop of the future” production layout
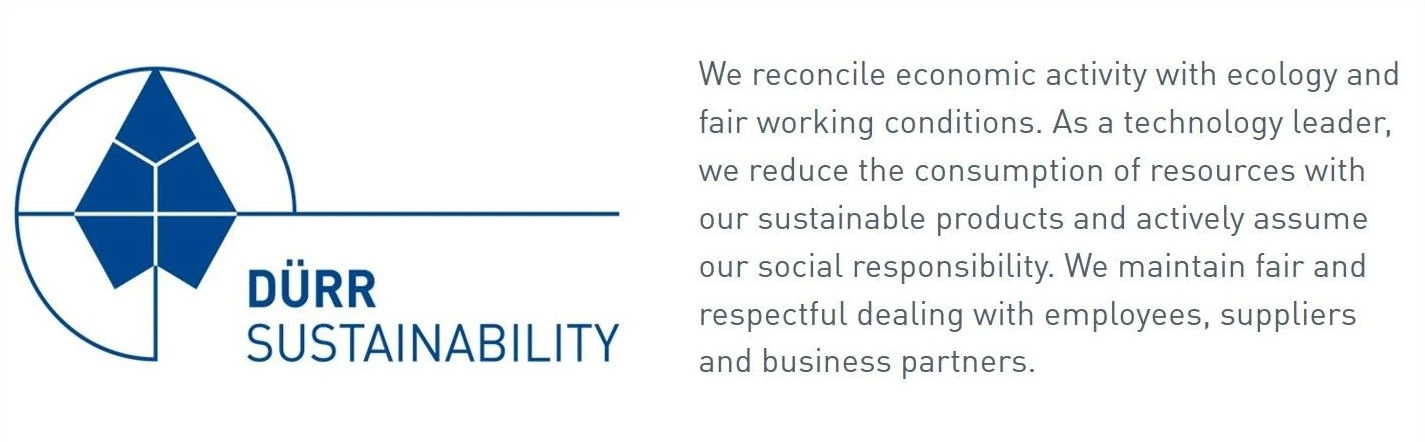