- durr.com
- >
- Products
- >
- Environmental technology
- >
- Exhaust gas and air pollution control
- >
- Sorpt.X – Sorptive processes
- >
- Sorpt.X CD/CC – VOC Concentration
Sorpt.X CD/CC – VOC Concentration
The adsorption process of the Sorpt.X CD/CC is used for concentrating the pollution content in the air.
The Sorpt.X CD/CC Air Pollution Control System is a tried-and-tested solution for continuously purifying large exhaust air volume flows containing low levels of solvents (VOCs) using adsorptive concentration with a downstream purification phase.
The Sorpt.X CD/CC is therefore based on the sorptive process. This process has a particularly good cost-benefit ratio when used for purifying large exhaust air volume flows with low pollutant burdens where a direct purification process, for example in a regenerative thermal Air Pollution Control System, would not be cost-effective.
Sorpt.X CD/CC benefits
- Low CO2 emissions and operating expenditure as a result of the high concentration ratio of up to 40:1
- Continuous desorption and treatment of pollutants without pressure fluctuations
- A long life span because of the high desorption temperature of up to 220°C (in continuous operation)
- Volatile organic compounds (VOCs) that boil at high temperatures can be removed using discontinuous or, in special cases, continuous hot gas desorption (up to a maximum of 300°C)
- The system has no moving parts except for the rotor which means that it requires little maintenance and is highly reliable.
- Can be combined with a variety of oxidation technologies
- Application-specific oxidation processes can be used without additional fuel
- Heat recovery is an integral part of the process
Operating principle Sorpt.X CD/CC
Sorpt.X CD/CC Air Pollution Control Systems concentrate the exhaust air volume flow. This reduces the volume of exhaust air to be processed in the downstream unit and increases its pollutant concentration.
Sorpt.X CD/CC Air Pollution Control Systems consist of an adsorption rotor, which is divided into an adsorption zone and a much smaller desorption and cooling zone. In the adsorption zone, the solvents removed from the exhaust air and transferred into the adsorbents. This happens because the pollutants are more soluble in the adsorbents. The adsorbents selected in advance to ensure that the pollutant dissolves more effectively than it does in the air. This makes it possible to separate the pollutants from the exhaust air volume flow.
The continuous turning motion of the rotor moves the adsorbed pollutants into the desorption zone, where they are desorbed (removed) by means of a hot desorption flow that is much smaller in volume. The concentrate air flow produced by the rotor has a correspondingly high solvent burden. It is then moved on to the next stage of the process where it can be purified much more efficiently.
Using an innovative approach, the Dürr Sorpt.X CD/CC Air Pollution Control System concentrate the exhaust air volume flow to a ratio of a maximum of 40:1 of its original pollutant content. As a result, the operating expenditure of the Sorpt.X CD/CC system is significantly lower than when using only a thermal process.
Application areas Sorpt.X CD/CC
Modular Sorpt.X CD/CC Air Pollution Control Systems primarily used in paint shops and surface treatment plants and in the printing, coating, and semiconductor industries. This Dürr product range is also found in the chemical industry and the plastic and composites industry. In addition, it is used for cleaning exhaust air from foundries.
- Paint Shops
- Printing & Coating Industry
- Semiconducteur Industry
- Chemical Industry
- Plastic & Composites Industry
- Foundries
Technical specifications Sorpt.X CD/CC
Depending on the application, each adsorber unit can treat exhaust air volume flows from 20,000 to 230,000 Nm³/h. The individual modules can easily be combined with one another, which means that an almost unlimited exhaust air volume flow can be cleaned. At present, more than 50 billion m³ of air are concentrated every hour in Dürr Sorpt.X CD/CC systems throughout the world.
Using an Sorpt.X CD/CC system, organic solvents including VOCs (volatile organic compounds) can be removed from exhaust air volume flows. Typical substances of this kind are:
- Aliphatic and aromatic hydrocarbons
- Alcohols
- Acetates
- Chlorinated hydrocarbons
- Glycols
- Aldehydes
- Ketones
Sorpt.X CD/CC systems are not suitable for formaldehyde, methanol, methyl chloride, highly acidic or alkaline inorganic components, sulfur compounds, halogens, heavy metals, plasticizers, or oil mist. The temperature of the exhaust air should not exceed 40°C and its relative humidity should not be greater than 85%. The exhaust air may therefore need to be cooled and/or dried before being processed.
Sorpt.X CD/CC systems can be used for exhaust air with a pollutant level up to 2 g/Nm³. If the level is higher than this, no concentration process is needed, because a direct thermal treatment, for example in a regenerative thermal air pollution control system, is more cost-effective.
Construction Sorpt.X CD/CC
The VOC concentration and oxidation systems designed and supplied by Dürr consist of the following main components:
- Modular Sorpt.X CD/CC adsorption rotor/turntable with an integrated filter compartment
- Central exhaust air extraction fan
- Downstream Oxi.X TR, Oxi.X RTO, Cat.X PLAir Pollution Control System to purify the concentrate air flow, recover heat from the air, and heat the desorption air
- Electrical switching, control, and monitoring system
- Internal connecting pipes with all the necessary shaped parts, flaps, compensators, and thermal insulation
At the heart of the Sorpt.X CD/CC system is an upright rotor divided into individual segments or a turntable with two adsorber blocks which are positioned one behind the other in the direction of flow of the air. The standardized modular design of the system makes it possible to choose from a wide range of concepts and adsorber materials for concentrating the pollutants.
The reliable turntable system also allows special carbon-fiber adsorber blocks or zeolite mixtures to be used. These have proved to be the ideal solution for concentrating pollutants in the chemical industry.
In most cases, however, the adsorbers consist of a ceramic carrier material with a honeycomb structure which is permanently impregnated with zeolites. The main advantage of zeolites over activated carbon is that they are resistant to high temperatures and not flammable. The honeycomb structure of the zeolite blocks keeps pressure losses to a minimum and also reduces the electricity consumption of the system. One or more integrated filters protect the adsorber material from becoming clogged or blocked by dust or paint particles and significantly extend the life span of the system.
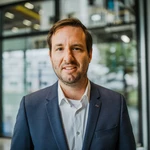
Carl-Benz-Str. 34
74321 Bietigheim-Bissingen
Germany
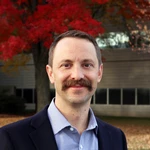
26801 Northwestern Highway
48033 Southfield, MI
United States