- durr.com
- >
- Products
- >
- Environmental technology
- >
- Exhaust gas and air pollution control
- >
- Oxi.X – Thermal processes
- >
- Oxi.X TR – Recuperative thermal oxidizer
Oxi.X TR – Recuperative thermal oxidation
The Oxi.X TR system is a recuperative thermal oxidizer that has been used for more than 40 years to remove a variety of pollutants from exhaust air. These systems are generally suitable for exhaust air volume flows of 1000 Nm3/h or more and use a thermal process.
Oxi.X TR benefits
- An adjustable heat exchanger ensures flexibility
- Energy consumption can be reduced by up to 15%
- The advanced burner can easily be replaced and offers maximum flexibility
- Low capital expenditure
- The robust design results in a long life span
- Small footprint and light in weight
- Incoming concentrations of up to 25% of the lower explosion limit
- Minimal maintenance
Operating principle Oxi.X TR
As in all thermal processes, the exhaust air is heated to a high enough temperature to oxidize the pollutants (hydrocarbons). This produces steam and carbon dioxide. In the Oxi.X TR Air Pollution Control System, the polluted air is initially heated by the hot clean air in the integral recuperative heat exchanger. This allows a large proportion of the combustion heat to be recovered.
When the air enters the combustion chamber, the burner heats it further to over 700°C. This starts the process of oxidizing the pollutants, which is completed after the exhaust air has passed through the chamber. The hot clean gases then pass into the exhaust air heat exchanger, which removes the heat and uses it to pre-heat the incoming exhaust air.
Before the treated exhaust air is released into the atmosphere, any residual heat is generally used by downstream heat recovery systems to heat thermal oil, hot water, or air or to generate saturated steam.
The consumption of primary energy in the oxidation process is typically highly dependent on the quantity and heating value of the pollutants. For this reason, natural gas, liquid gas, heating oil, and other organic fuels can be used as supplementary fuels in the Oxi.X TR Air Pollution Control System.
Application areas Oxi.X TR
The recuperative thermal oxidation process is particularly cost-effective when the energy extracted from the clean gas by downstream heat recovery systems can be reused in the production process. As a result, the Oxi.X TR system is widely used for Air Pollution Control in drying processes, because a large amount of energy is needed to operate the dryer.
The system is used in almost all types of painting processes throughout the world, from vehicle bodies and small automotive components through to flooring and wallpaper. These industries often make use of coatings or paints that contain silicon. In the case of these materials, the effective thermal oxidation process and the relative insensitivity of the Oxi.X TR system to silicon dioxide (SiO2) deposits are major benefits.
Technical specifications Oxi.X TR
The Oxi.X TR (recuperative thermal oxidation) system is designed for exhaust air volume flows of between 1000 and 40,000 Nm³/h. It is ideal for plants with secondary heat recovery systems and is particularly cost-effective where there are only moderate levels of pollutants. The Air Pollution Control System oxidizes the pollutants in process exhaust air at temperatures between 680 and 740°C. It used for Organic pollutants.
Construction Oxi.X TR
The Oxi.X TR compact unit essentially consists of the combustion chamber, the burner, and the integral heat exchanger, which is used to pre-heat the exhaust air. Dürr Oxi.X TR Air Pollution Control Systems have a scalable design which gives them a long life span and keeps maintenance to a minimum. The burner can be specially adapted to your requirements and can also be replaced at any time.
Find out about other features of Oxi.X burner technology.
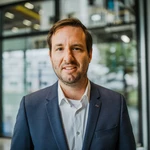
Carl-Benz-Str. 34
74321 Bietigheim-Bissingen
Germany
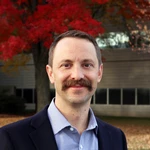
26801 Northwestern Highway
48033 Southfield, MI
United States